Blog
- Details
- Written by: interGen Support
This video, “Honoring Our Ancestors by Sharing History,” features the Santa Cruz Evergreen Chinese Memorial.
Video created by Andrew O’Keefe and is shared here with permission. Learn more about Andrew’s work at www.andrewjokeefe.com
- Details
- Written by: interGen Support
Tom Ralston Concrete worked with 3-other contractors on the day of this pour; over 50-finishers poured out over 8-trucks from 6:00 a.m. to 9:00 p.m. Piping concrete down a hill and spraying it onto a dome-shaped house.
Thanks to our friends at Levy Media Works for capturing beautiful aerial video of the community projects completed by Tom Ralsto Concrete throughout Santa Cruz. Check them out on their website and Instagram!
- Details
- Written by: interGen Support
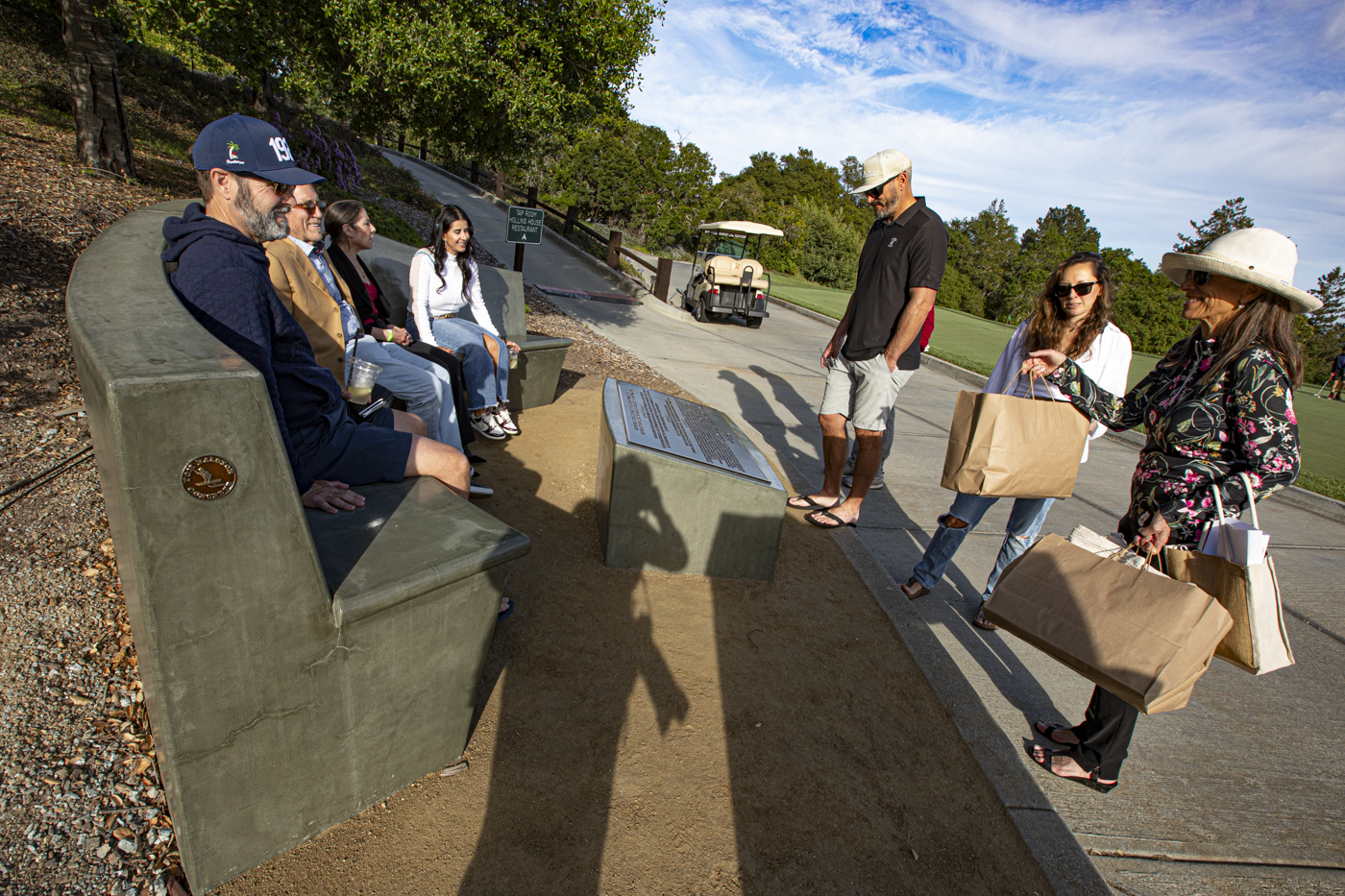
On April 11, 2025, Pasatiempo Golf Club in Santa Cruz, California unveiled three bronze statues honoring golf course developer Marion Hollins, her dog Carlos, and course architect Dr. Alister MacKenzie. The installation was commissioned by the Pasatiempo Historical Foundation, led by Chair Linda Sorensen and Vice Chair Emily Chorba.
Tom was selected to design several key elements for the site:
-
A custom donor bench featuring a sloped back and tilted seat with integrated drainage and custom colors. The bench was strategically placed to offer clear views of the first tee and sweeping vistas of Monterey Bay.
-
Two stone plinths to support bronze donor recognition plaques
-
A poured pad for the life-size bronze statues
-
An informational kiosk sharing the historical significance of Pasatiempo and its founders
- Details
- Written by: interGen Support
Our friends at Levy Media Works captured some beautiful aerial video of the community projects completed by Tom Ralsto Concrete throughout Santa Cruz. Check them out on their website and Instagram!
View this post on Instagram
- Details
- Written by: interGen Support
Our friends at Levy Media Works captured some beautiful aerial video of the community projects completed by Tom Ralsto Concrete throughout Santa Cruz. Check them out on their website and Instagram!
Last stop on a drone tour of some the the communitu projects completed by @tomralstonconcrete in Santa Cruz, we arrive at Pleasure Point on the east side.
An amphitheater incorporates beautifully colored concrete with real sea shells, beach glass, shark teeth and fossil replicas from the Monterey Bay.
The main embed was a replica of a 5-million year old whale bone that was located in May of 2010 approximately 500 yards south of the amphitheater.
The terraces mimic the geology of the ocean shelves of Monterey Bay. As one sits on the concrete ‘shelves’ you have an uninterrupted view of surfers riding the Pleasure Point waves.
This is a great spot to meet up with friends or family, walk the dog , push strollers, people watch or catch a sunrise. 🌅
- Details
- Written by: interGen Support
Our friends at Levy Media Works captured some beautiful aerial video of the community projects completed by Tom Ralsto Concrete throughout Santa Cruz. Check them out on their website and Instagram!
Next up on a drone tour of some of the community projects completed by @tomralstonconcrete in Santa Cruz, we are leaving the west side and heading to midtown to the @riotheatresantacruz — a historic landmark built in 1949, with a unique “cycloramic” screen which gave a wrap-around panorama and illusion of depth.
A new green color-infused concrete sidewalk with a red curb + gutter, and three bronze safety bollards were installed at the front entrance. Embedded in the concrete is the Rio Theater’s logo and a historical plaque featuring Laurence Bedford’s profile, both cast in bronze.
Local singer-songwriter Tom Ralston’s Band will play a benefit concert for @secondharvestsantacruz on Saturday December 2, 2023 at the Rio Theater, from 7pm - 10pm. The band has a unique sound incorporating jazz, soul, and rock, with his 14-piece ensemble with string and horn section.
- Details
- Written by: interGen Support
Our friends at Levy Media Works captured some beautiful aerial video of the community projects completed by Tom Ralsto Concrete throughout Santa Cruz. Check them out on their website and Instagram!
Next up on a drone tour of some of the community projects completed by @tomralstonconcrete in Santa Cruz is Evergreen Cemetery — one of the oldest cemeteries in California, created in 1858.
A new ADA pathway was created that allows everyone to access the cemetery’s grounds. A Chinese Gate ⛩️ commemorates Chinese immigrants who lived and worked in Santa Cruz. As I was filming, a dark-morph red-tail hawk was seemingly keeping guard on top of the gate.
- Details
- Written by: interGen Support
Our friends at Levy Media Works captured some beautiful aerial video of the community projects completed by Tom Ralsto Concrete throughout Santa Cruz. Check them out on their website and Instagram!
Let’s continue a drone tour of some of the community projects completed by @tomralstonconcrete throughout Santa Cruz.
The Surfer Statue stairs allow surfers another access point to the ocean and helps them get in and out of the water.
Cowell’s stepping stones park provides a viewing area for tourists and locals alike to watch the surfers. Kids have a place to play and jump between the rocks.
The roundabout at the entrance to the Santa Cruz Wharf, Beach St. and Pacific Ave. join together in a continuous flow of traffic, instead of having a 4-way Stop or traffic lights. In the center there is a pod of stone dolphins.
- Details
- Written by: interGen Support
Our friends at Levy Media Works captured some beautiful aerial video of the community projects completed by Tom Ralsto Concrete throughout Santa Cruz. Check them out on their website and Instagram!
Let’s take a drone tour of some of the community projects completed by @tomralstonconcrete throughout Santa Cruz. The Princes of Surf plaque at the Santa Cruz Surfing Museum pays homage to the three princes who rode Santa Cruz waves in 1885, the first known instance of mainland surfing. The Steamer Lane stairs were replaced and a concrete path (“Wally Pads”) was poured along the base of the cliffs, to help surfers get in and out of the water.
- Details
- Written by: Tom Ralston
Tom Ralston is friends with Thom Zajac who owns the Comic News. Tom and Thom had lunch together one day and talked about an ad for the Comic News that would be in the vein of comedy. Tom Ralston who has a reputation for being humorous thought it would be fun to spin off a series of cartoons for both the Comic News and Tom Ralston Concrete. Tom is has been engaged in creating decorative concrete for over 30 years, with song writing, leading a band and producing musical shows; but now dips his hand into some original “concrete comedy.”
- Details
- Written by: TRC Staff
Tom Ralston was honored this February 2016 with Santa Cruz’s prestigious Gail Rich Award. Here is the video of the ceremony where Paul Meltzer introduces Tom (at 3:43). Paul considers himself the Dr. Watson and Tom is his Sherlock Holmes. Many will smile when they hear Paul's humorous account of Tom's life, his music, his art, and how all of these are somehow intertwined in his concrete work.
Tom's speech demonstrates how he does all things: with lots of determination, energy and passion (at 8:49). Tom shares his anecdotes while recognizing his friends who have inspired him and expresses how he is touched, humbled, and honored to receive this highly regarded award. Tom runs out of time while thanking (at 16:10) his children, the people in his band, and all in his company.
You really have got to take a listen. The roar of laughter in the background tells us that Tom wasn’t the only one having fun at The Gail Rich!
- Details
- Written by: Tom Ralston
It was an incredible honor on a beautiful Santa Cruz day when the SCPD gave plaques to all who helped construct the Fallen Officers memorial. The tragedy of fallen officers Butch Baker and Elizabeth Butler rocked the entire Santa Cruz Community and will never be forgotten. We were grateful that we could contribute our services to the memorial.
L-R Deputy Chief Steve Clark, Tom Ralston, Police Chief Kevin Vogel, Assistant Police Chief Rick Martinez
- Details
- Written by: Tom Ralston
Wow…all I can say is “Wow”!!
I received a visit from Sentinel journalist/writer Wallace Baine a week ago and he said that I was chosen to be a recipient of the esteemed Gail Rich Award. The award celebrates the spirit of arts in Santa Cruz by “recognizing those who inspire our diverse and culturally rich community”.
My friend Jeff Luhn who is a musician, photographer and conceptual artist had an idea for my upcoming CD release. His idea was to cover half of me with cement and leave the other half alone. I donned a tuxedo to provide an distinct yin-yang. Awesome idea!!
I mentioned this to the amazing photographer, Shmuel Thaler has been photographing the Gail Rich Award honorees (and countless other subjects and events) since its inception and thought the idea was awesome as well. Here are a few of the behind the scenes shots that I wanted to share with my friends on my blog.
- Details
- Written by: Tom Ralston
Tom Ralston Concrete has built quite a few very cool and interesting concrete and masonry pieces for Santa Cruz County. However I could make a strong case that to date the Chinese Monument that TRC built in 2014 in the Santa Cruz Evergreen Memorial is the most meaningful and significant.
There were many that contributed to the idea, the vision, and to the construction of the Chinese Memorial. The George and Emily Ow Family primarily funded the project. The Museum of Art and History helped to generate momentum and was led by Director Nina Simon. Nina's husband Sibley diligently worked with volunteers and organized labor to help pull the project together. The initial monument concept and inspiration was from Geoffrey Dunn and George Ow who met with me to begin brainstorming ideas for the memorial.
The Chinese that were buried in the Evergreen Memorial were immigrants that came to California and Santa Cruz to escape rebellion and civil war; but also to fulfill a dream of prosperity and to make a better life for their families. To paraphrase historian Sandy Lydon: the contributions that the Chinese made were fundamental to the region's economic development they were not treated as such. As history tells us many if not most of the Chinese settlers were treated like second rate citizens there are ample examples of gross prejudice.
Again from Lydon in his book Chinese Gold "No Monuments, no prominent place names, no gilt "Chinese-style" buildings, and no large concentrations of Chinese people attest to the presence [and contributions made] in the Monterey Bay Region."
Now, with the Chinese memorial built in the Evergreen Cemetery, there finally is a place that people can honor and memorialize the Chinese settlers. Last year on April 5, 2014 the Santa Cruz Museum of Art and History organized a funeral procession that started on Front Street near Old Chinatown and ended in the Chinese section of the Evergreen Cemetery. Along the way the procession was joined by Chinese "lion dancers" who provided a very colorful addition to the Chinese celebration.
My vision for the concrete memorial was carried out by TRC's dedicated and hardworking crews and were led by master carpenter Rex Nicoliason. The structure, which was all poured together with a special colored SCC (self-consolidating concrete), when fully cured will be in excess of 8,000 PSI. Regular concrete starts at about 2500 PSI. Sean Monaghan who has partnered with me on many creative projects over the last 2-decades cast some incredible solid bronze headstones that had names of Chinese actually buried in Evergreen. The headstones were originally made with simple wooden 2 x 12's which had the deceased names carved into them. Sean beautifully replicated the wooden headstones with bronze and had his student, Yue Yu, provide the translation and calligraphy for the headstones. Ralph Royer and Josh Roton of RCR fabrication made exacting Chinese characters that were later powder coated a brilliant red. The red characters played beautifully off of the charcoal colored concrete. The translation and poetry for the monument was provided by Professor Yuming Shang. Other local contractors that contributed to making this happen was Landscape Contractor Randy Quilici, Lewis Tree Service, E Clampus Vitus Branciforte Chapter 1797, The Landscape Company, Homeless Services Center, Y.E.S. High School and many other volunteers.
Sibley Simon who is the chairman for the Evergreen Cemetery committee for the MAH took the lead for overseeing construction and making sure that the Cemetery was cleaned up and ready to go for the Quing Ming Festival or "Tomb Sweeping Day". According to George Ow in Chinese folklore, "if something is not settled during a lifetime, you have hungry ghosts, like angry spirits." Barring a nuclear warhead striking the memorial with a direct hit the structure will stand for thousands and thousands of years, forever feeding and pacifying the hungry ghosts.
I will be forever grateful for being asked to create such an important and significant monument. My thanks go to all!
Tom Ralston